The COVID-19 pandemic has caused disarray in just about every corner of society, including Australia’s industrial sphere. Both the manufacturing sector and the industrial real estate market have raced to respond to the pandemic’s pressures, and many of these changes will be long-term. Below, I look at what moves the sector is making to become stronger in the face of global crisis.
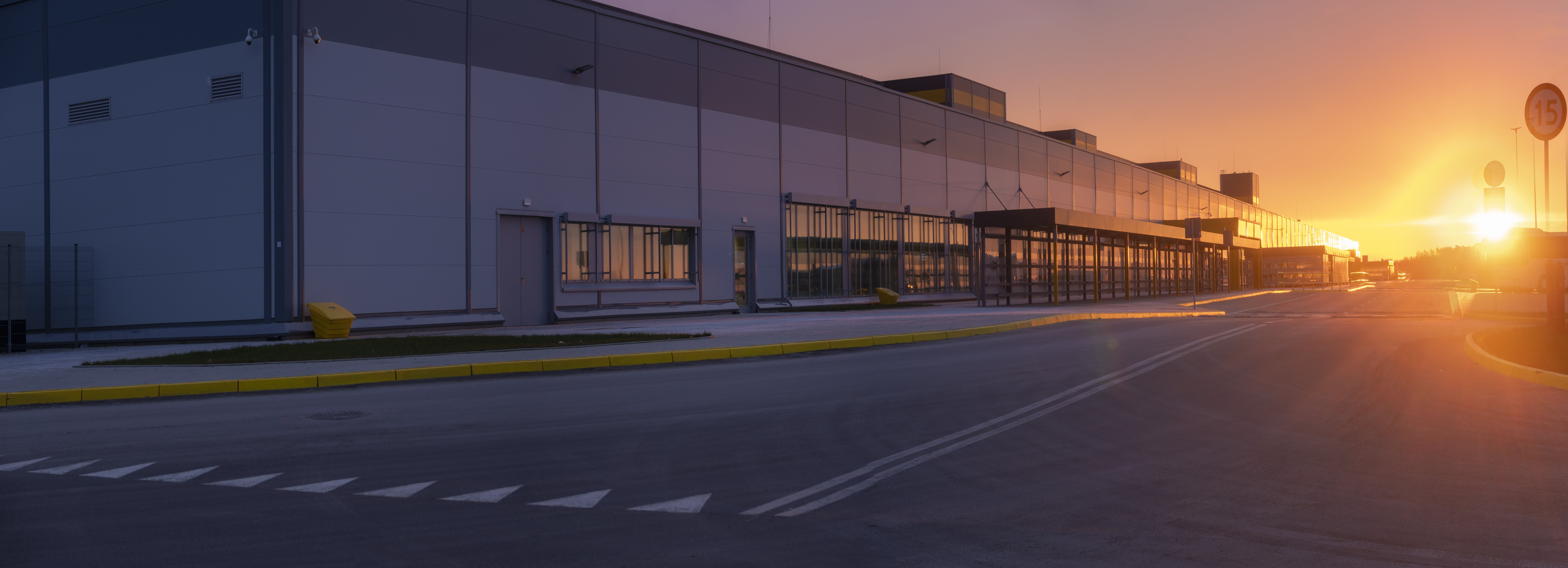
What are the Consequences for the Manufacturing Industry?
It has been 6 months since the coronavirus first appeared, and the time since then has been tumultuous. Industrial and logistics suffered seismic disruptions as China’s shutdowns created an enormous backlog: material exports to the country were halted, and part and product imports from China were put on hold.
Given that the majority of the world’s supply chain relies on Chinese manufacturing, these cutoffs created widespread disorder in the manufacturing sectors of most nations, including Australia. Without Chinese shipments available, the country realised that it didn’t have sources for many important goods.
This sparked rapid adaption. Australian manufacturers rushed to modify their operations so that they could produce ventilators, medical personal protection equipment (PPE), and other urgently-needed products.
Rising to the occasion was a triumph, but it was also a grim awakening. The crisis exposed the lack of independence in Australia’s manufacturing sector. Where once manufacturing had produced 30% of the nation’s gross domestic product (GDP), it had now fallen to just 6%. Entire industries were crippled by the lack of local manufacturing, and lives were even put at risk because of it.
Post-COVID Impact on the Industrial and Logistics Development Market
As manufacturing was rattled by the coronavirus, so too was industrial development and real estate. However, there were some areas in which the sector showed strength.
Commercial and retail tenants at this time struggled to pay their rent. Yet, most industrial tenants were able to make rent despite the disruption. Where industrial companies were hurt though was in their plans to move: many businesses put a hold on moving into new facilities, especially when the pandemic first took hold.
With new tenancies down, industrial real estate has had no choice but to make accommodations. Many have lowered their lease terms down to 6 months. Such a short term is desirable not only for businesses with an uncertain outlook, but also for those who are dealing with a backlog of overseas shipments.
Storage Warehouse Demand is Rising
Quite a number of companies, particularly in logistics, need temporary warehouse space to hold a massive influx of packages that were delayed by the virus shutdowns. Store suppliers have also found themselves in similar circumstances, as their client shops are no longer selling at their usual rate.
Additionally, a sharp increase in online shopping has created a pressing need for warehouse space from new and expanding eCommerce stores, as well as existing traditional retailers who have had to switch focus to online sales. These types of businesses have been urgently looking for industrial units that can store their growing inventory and shipment packages.
Virtual has Become the New Normal
The changing nature of property demand isn’t the only thing industrial developers have had to adapt to. They’ve also had to find ways to work around pandemic restrictions without compromising service. More in-person property viewings and purchase meetings are now being transitioned to the virtual sphere. Other pre-sale or pre-investment activities such as property surveying and subdividing are also being performed digitally.
Embracing virtual modes for traditional operations is one of the key ways industrial real estate is managing to keep their customers safe without undermining the availability of their service. This is ensuring that manufacturing businesses (literally) have the room to grow as they take on more domestic production.
Moving Forward by Building Resilience
Achieving recovery isn’t about returning to pre-virus levels of production and operation. Rather, it’s about changing industrial and logistics to safeguard against similar crises in the future. Manufacturing leaders have been forced to take a hard look at what changes need to be made to ensure smarter resource planning and greater market independence.
Australia’s Federal Government has established a manufacturing task force to develop these insights. It is part of the commission headed by former Fortescue Metals CEO, Nev Power, to find ways the Australian economy can adapt in the wake of COVID-19.
The manufacturing task force’s leadership has expressed significant criticism of Australia’s over-reliance on foreign supply chains. There’s been talk of reducing offshoring and exports in a number of sectors where Australia has a distinct home advantage, such as the production of lithium products.
This focus on expanding domestic manufacturing will open up many opportunities down the road, and increase demand for industrial and logistics development.
Keep Your Business Strong with Top-Tier Talent
The most resilient names in industrial and logistics real estate development are those that make sure they’re armed with the most capable teams. Whether you’re looking for gifted Development or Project Managers or an Asset or Facility Manager who can guide your enterprise and your tenants toward expansion, we can connect you with the talent you need
Related Articles:
Open Banking is Here - What it Means for Australian Banks and Their Talent Pipeline
PURPOSE=PROFIT How to give your brand purpose to attract customers and employees